How Demand Planning Can Improve the Supply Chain
Last Updated July 26, 2023
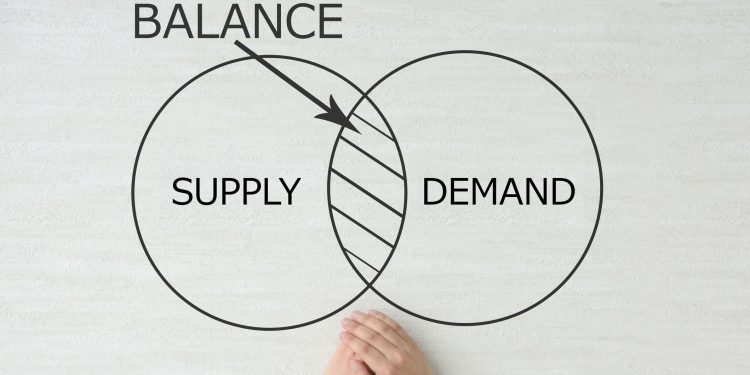
To maximize profitability, supply chains need to be as efficient as possible. Accurate demand planning is critical in ensuring supply chains are efficient for inventory and, ultimately, revenue.
What is Demand Planning?
Demand planning is a supply chain management process of forecasting, or predicting, the demand for products to ensure they can be delivered and satisfy customers. The goal is to strike a balance between having sufficient inventory levels to meet customer needs without having a surplus. A wide variety of factors can influence demand, including labor force changes, economic shifts, severe weather, natural disasters or global crisis events.
What are the Aspects of Demand Planning?
Demand planning spans several aspects, with the three primary areas being:
Product Portfolio Management
Product portfolio management oversees the overall product lifecycle, beginning with the introduction of a new product through to its end-of-life planning. In many cases, product lines are interdependent, and understanding how new products may influence demand for other products is important to understanding the overall product mix required to maximize market share.
Statistical Forecasting
Using historical data, statistical forecasting creates supply chain forecasts with advanced statistical algorithms. In this area, it is important to determine the accuracy of each model, identify outliers and exclusions and understand assumptions. Seasonal shifts (think the spurt of holiday shopping that occurs between October and December for retailers, or the boost in yard equipment sales in spring months) can also be assessed with statistical forecasting.
Trade Promotion Management
Trade promotion or marketing events can influence demand, especially in the retail industry. The goal of a trade promotion is to help a brand connect with a customer, often through an in-store giveaway, discount, or promotion, and these events can impact the demand for a product.
Why is Demand Planning Important?
If product isn’t available for customers to purchase because it’s out of stock, businesses lose out on revenue, and over time, they could lose the customer to a competitor. On the other hand, sitting on a slew of unused inventory incurs both space and production costs unnecessarily. With demand planning, business leaders can stay in front of market shifts and make more proactive decisions, while being responsive to their customers’ needs.
Best Practices for Demand Planning
Demand planning is a multi-step process, dependent on the right tools, information and processes. Often, there can be unique nuances in the process, based on product positioning, inventory needs and organizational goals, but some best practices to keep in mind include:
Implement the Right Software
There is a plethora of options when it comes to enterprise resource planning (ERP) systems, so choosing the right one can be tricky. When considering ERP software, it’s important to examine the ability of the tool to handle forecasting nuances as well as the provider’s reputation, reporting capabilities, and the transparency and reliability of the forecasts it produces.
Gather and Prepare Data
Data drives demand planning, now more than ever. Real-time visibility into inventory movements coupled with metrics reports that paint a clear picture and data mining and aggregation that can identify areas for improvement or reaction can help to create more agile process modelling.
Define Process Models
Lacking a defined process for a demand planning cycle leads to chaos. Confusing process with information that is simply a set of widely known facts around an organization is all too common, making it difficult to hold anyone accountable, and thus hurting overall performance. For most companies, the steps in the demand planning process go something like this:
- Preparation of data
- Initial forecasting
- Incorporation of market intelligence
- Consideration of sales goals and financial reports to reconcile bottom-up forecasts with top-down financial and sales forecasts
- Refine a final forecast
- Performance monitoring based on real-time analytics
Implement and Monitor
Successful demand planners usually design a pilot version of the plan using historical data, or descriptive analytics, as a basis. They also make regular adjustments and have a team of people dedicated solely to devising the plan, implementing it, reducing error and bias, and designing processes for execution.
The Future of Demand Planning in the Supply Chain
Like many business needs, supply chain and demand planning are going digital. Advances in applications of machine learning within the supply chain are making it possible to adapt and update forecasts in real time, allowing inventory to run leaner, without missing the mark on demand.
For supply chain professionals, understanding how to use digital enterprise architectures and implementing artificial intelligence and machine learning programs that can help optimize a lean, agile and data-driven approach will reveal new ways to cut costs in operations, boost revenue and offer a greater competitive edge.
A better-connected supply chain means demand planning can be conducted even more in the moment. When implemented well, demand planning can be a pivotal process in boosting a supply chain’s profitability.